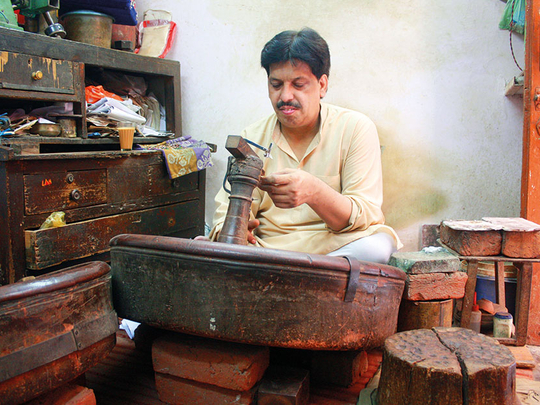
NEW DELHI The jewellery making industry in India is racing along the expanding arc of technology but in this race is one artisan who remains steadfast in his love for the time-brunished, traditional methods of jewellery making. Azhar Ahmed still uses the classic methods and tools of the trade that existed centuries back to make gold necklaces, bangles, bracelets and other ornaments to produce stunning pieces of jewellery.
The tiny room from where 42-year-old Ahmed operates is located on Gali Sayyedan at Pahari Bhojla in the Walled City, now famous as Old Delhi. It is a residential colony situated in a lane opposite the majestic Jama Masjid’s Gate No.1. The area has its own legend as ornamentation: the pahari (hill) is named after a notorious dacoit Bhojla. It is believed that the dacoit operated from this hill before Mughal Emperor Shah Jahan decided to shift his Capital from Agra to Delhi. While everything about the place changed since, Bhojla’s name endures.
Ahmed’s workshop, which is part of his house, can be reached only on foot, as even a cycle rickshaw is unable to enter the narrow bylanes in the area. The tiny room is filled with tools for hand-crafted jewellery that are rarely seen these days of computerised techniques. Jewellers of today could well be amazed at Ahmed’s allegiance to the equipment that harks back to the decades gone by.
When Gulf News drops in to meet Ahmed, he is engrossed in examining a piece of artificial jewellery whose design is what goes for fashion these days. “Gone are the days when there was a huge volume of work in gold and silver jewellery,” he laments. “Now, only a few jewellers and suppliers who still value traditional hand-made artisanship place orders with me,” he says. That apart, women from the neighbourhood also approach him with orders for pieces of jewellery. “It keeps the home fires burning,” he adds.
He proudly points the strange-looking tools and paraphernalia around him. “I work with these tools that have largely disappeared with the times,” he says.
He is sitting in front of a round, hollow-looking piece of equipment called kunda, that is integral to jewellery carving. Though made of stone, it appears to be of wood. “Yes, everyone thinks the unit is made of wood. It must be some hundred years old and belonged to my guru, who inherited it from his guru. I can safely say it’s an antique,” Ahmed says.
The kunda was made by potters who made earthen vessels, but out of about 10 such huge basins, only two or three would survive on being heated and treated. “No one makes it anymore, as it requires hard work,” Ahmed says.
The kunda has a raised block attached to it, which is used as a platform on which to carve jewels. Different kinds of hammers and tongs form an essential part of the job of carving design on to the gold, especially to hold and fold a half-finished product of jewellery. While chisels, pincers and saws are used to cleave the metal, punches and gravers are used to create design on the ornaments. A number of decorative motifs are created with the help of these instruments. Casting and hammering of ornaments is also done on the spot.
Ahmed demonstrates the use of a narrow drill to create spaces in a gold item, which are then filled with bits of finely carved glass or stones to lend it the embellishment. Adjacent to him, Ahmed’s lone employee, Raja, has just finished working on a necklace that is placed on what is called a hundi (wooden platform) that looks like a stone slab. Admiring the necklace, Raja discusses the design with his master as he prepares to extend the strings on the necklace by adding beads to them.
All [my children] are studying in English-medium schools and are keen to take up other jobs. People have no respect and fondness for this work anymore.”
- Azhar Ahmad | Traditional jeweller
India’s gem and jewellery industry contributes seven per cent to its overall GDP (Gross Domestic Product) and 15.7 per cent of its merchandise exports, as per India Brand Equity Foundation, an agency under the federal commerce ministry.
With the introduction of multiple design and manufacturing techniques, the face of the jewellery industry has totally changed. Even the conventional pen and paper drawings have been eclipsed and digitised designs are in vogue. But Ahmed confidently continues to use primitive methods to create masterpieces comprising intricate and delicate motifs.
“In India, jewellery does not just hold traditional and aesthetic value; it is also considered as a source of security in times of financial crisis. Earlier, women wore heavy jewellery, but now contemporary jewellery that is lighter in weight, is popular among women,” Ahmed informs.
So, what inspired him to become a goldsmith? “My father Mohammed Ismail was a chef at Karim Hotel, considered one of city’s most famous culinary destinations. He was keen that his children enter different professions. Realising that all cultures throughout history have been making and wearing jewellery, he chose this field for me.
“Traditionally, jewellery-making skills had been passed along through apprenticeship to the next generation in the family. Unlike present times, when universities and colleges offer courses as a part of their fine arts curriculum, we specialised mainly by observing and then learning the techniques through trial and error methods,” Ahmed discloses.
Ahmed began to learn jewellery making at the age of 11. “It takes several years to learn this art,” he says. “A goldsmith must be skilled in workmanship, which includes filing, soldering, sawing, casting, and polishing the metal. Even after more than 30 years in the field, my enthusiasm has not waned.”
Will any of his children follow in his footsteps? He has four children.
“No,” Ahmed is quick to respond. “All of them are studying in English-medium schools and are keen to take up other jobs. People have no respect and fondness for this work anymore.”