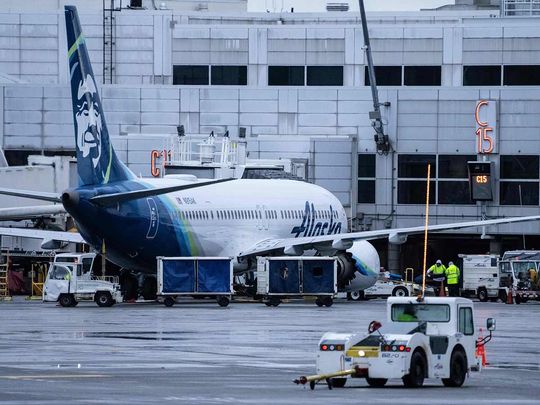
The fuselage section that ripped away from a Boeing Co. 737 Max jet midflight on Friday reflects a design feature in use for many years, suggesting investigators are likely to zero in on quality issues rather than a design flaw.
The Max 9 aircraft was built with a modular cutout in the frame that can house an emergency exit. Some airlines order planes with the doors installed to maximize the number of seats. Others, like Flight 1282 operator Alaska Airlines, don't require the extra exits and have the holes permanently plugged up.
From the inside, a plug is undistinguishable from the sidewall on the aircraft, while on the outside, an outline of the opening can be seen. The Boeing 737 cutouts date back to the mid-2000s, and hundreds have been installed.
"This has all the earmarks of a manufacturing deficiency, a quality escape from Boeing," said aviation safety expert Jeff Guzzetti, the Federal Aviation Administration's former accident investigation chief. "We can't help to not look at this recent event in the context of all the problems that Boeing has had with manufacturing quality deficiencies."
Cutouts like the one in the Alaska Air incident are aimed at increasing production efficiency and making seating arrangements more flexible.
They allow manufacturers to make one standard fuselage section, instead of tailor-making different designs for various airlines. This reduces complexity and cost, and facilitates changes in future. For example, a low-cost carrier purchasing the aircraft second-hand would be able to restore the exit and add seats.
The Alaska Air Max 9 was delivered in late October. The blowout occurred shortly after takeoff from Portland, Oregon for a flight to Ontario, California. It reached an altitude of about 16,000 feet before turning around and landing safely after being in the air for about 20 minutes.
Fuselages for the model are made by Boeing's biggest supplier, Spirit AeroSystems Holdings Inc.
In the wake of Friday's incident, Alaska Air has grounded all 65 of its Max fleet, a major setback for Boeing after working to get past manufacturing defects and costly repairs in recent years, many of them supplier-driven.
Last year Boeing slowed deliveries to fix misaligned drilling holes in the rear section of the 737. Most recently, the FAA said it's monitoring targeted inspections of the 737 Max to look for a possible loose bolt in the rudder control system.
Boeing's Max 9 and the coming Max 10 both are manufactured with emergency door cutouts. The Max 9 is certified to seat up to 220 passengers, which would require 10 emergency exits "- five on each side. However, most airlines want cabins that are less dense, to accommodate higher-paying passengers.
Alaska Air seats 178 people in its Max 9 jets, including 24 in what it calls premium class with 4 inches of extra legroom, and 16 in first class. United United Airlines Holdings Inc., the biggest operator of the Max 9, offers 179 seats across three classes and also plugs the emergency door cutouts.
Boeing began installing door cutouts in 2006 with the previous-generation 737-900ER. European planemaker Airbus SE also uses modular door designs in some of its A321 narrow-body aircraft.
Investigators will have to look into how the doors are plugged and why they exist if they can come open, said Richard Healing, a former National Transportation Safety Board board member.
"It's going to be serious engineering work and maintenance work, and certainly an opportunity for NTSB to dig in on this, and the FAA as well," said Healing, who is chief executive of consultant Air Safety Engineering. "My sense is that this is just the beginning of something."