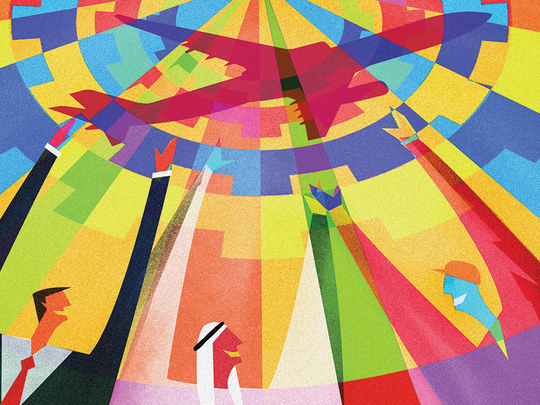
One of aviation’s earliest pioneers, the great Arab polymath, Abbas ibn Firnas, reportedly used feathers to build a rudimentary flying contraption in the ninth century. While there is no conclusive evidence that he succeeded, it is notable that he apparently realised the need to use lightweight, aerodynamic materials to build his flying machine.
Over a thousand years later, today’s flying machines would probably have been beyond ibn Firnas’ wildest imagination. But, as sophisticated as modern aviation is, its beginnings were simple.
Visionaries, such as the Wright brothers, doggedly pursued the dream of manned and powered flight at the turn of the 20th century with self-built craft. In fact, the Wright Flyer was, by current standards, a simple powered glider constructed with wood and muslin.
But, the impact of this era in aviation’s history is indisputable. Having proved that powered flight was possible, it served as a catalyst for the creation of the aviation industry. Having ruled out metals because of their weight and tendency to corrode, early pioneers such as William Boeing built their airframes out of lightweight spruce, birch plywood or balsa wood, and then covered them in fabric.
While aluminium was used in the piston engines that powered these planes, the possibility of an all-metal aeroplane didn’t become a reality until Alfred Wilm, a German physicist, developed a new, lightweight alloy called duralumin. It was this radical new material that allowed Hugo Junkers to build the world’s first all-metal aeroplane, the J-7 fighter, which first flew in 1917, and the F-13, the world’s first all-metal commercial aircraft, which was unveiled three years later.
From then on, the use of metal alloys enabled new performance improvements that would simply not be possible with wood and fabric airframes. The use of metals that were capable of handling the stress of flight, combined with the Monocoque principle — which used the skin of an aeroplane to support its structural load, not unlike an eggshell — enabled the development of the Boeing 247 in 1933.
It was the world’s first modern airliner, leveraging the strength of its anodised aluminium skin to maintain airframe integrity.
This, in turn, paved the way for cabin pressurisation and, in 1938, the Boeing Model 307 Stratoliner became the first commercial aeroplane to offer a pressurised cabin. With this development, long-range, trans-ocean air travel became a reality.
By the 1950s, the first generation of passenger jets, such as the de Havilland Comet and the Boeing 707, took to the skies. The all-metal airframes made it possible to comfortably fly passengers and cargo across unprecedented distances, creating the global airline industry.
While the 707 served as the engineering template for subsequent aircraft models, it was the iconic 747 — nicknamed the ‘Queen of the Skies’ — that represented the next major leap forward in aircraft design. Made possible by reinforced aluminium alloys, the original ‘Jumbo Jet’ featured a distinctive humped upper deck, the highest capacity passenger cabin and a bigger cargo hold than any aircraft at the time.
However, working with aluminium presented its own challenges and airlines sought out lighter, stronger and more fuel-efficient aircraft. In response, engineers began looking at other materials, such as carbon fibre composites and metals such as titanium, to reduce weight, drag, corrosion-related fatigue and operating costs, while improving the cabin experience.
The launch of the Boeing 777 marked one of the first significant efforts to increase the use of composites in commercial aeroplanes. Composites currently account for 12 per cent of a 777’s structural weight, including its vertical and horizontal tails, and the cabin floor beams.
But it is the Boeing 787 Dreamliner that truly defines the future of commercial aviation by bringing the benefits of composites for passengers, airlines and the environment. It is the first airliner to be built using composite barrel sections, doing away with the traditional aluminium sheets and the thousands of rivets needed to fasten them together.
As much as 50 per cent of the aeroplane is built from advanced composite materials, while a further 15 per cent is titanium. In fact, only 20 per cent of its airframe is aluminium, one of the many factors allowing airlines to dramatically reduce operating costs — through lower maintenance needs and improved fuel use — while boosting revenues.
Few industries have seen rapid innovation at the pace that the aviation industry has. In the span of just over a century we have evolved from wood and muslin machines capable of flying a few hundred meters, to the Dreamliner family, which, in its stretched 787-10 version, will be able to fly over 300 passengers and many tonnes of cargo across distances that Abbas ibn Firnas could only have imagined.
As this innovation evolves, one can only imagine what the future holds.
The writer is Vice-President of Commercial Airplanes Product Development at Boeing Commercial Airplanes.